Advanced Seal Design and Seal Stack Solutions
Material & Design Solutions supplies quality thermoplastic, elastomeric, and metal components for the oil & gas, fluid handling, and semiconductor markets, providing our customers with the advanced sealing solutions they need for various critical service applications. Our advanced seal stack solutions include:
- Custom Seal Assemblies
- Vee Stacks using High-Performance Materials
- T-Seals (Petroz, FKM, AFLAS, HNBR)
- Specialty O-Rings
- Spring Energized Seals
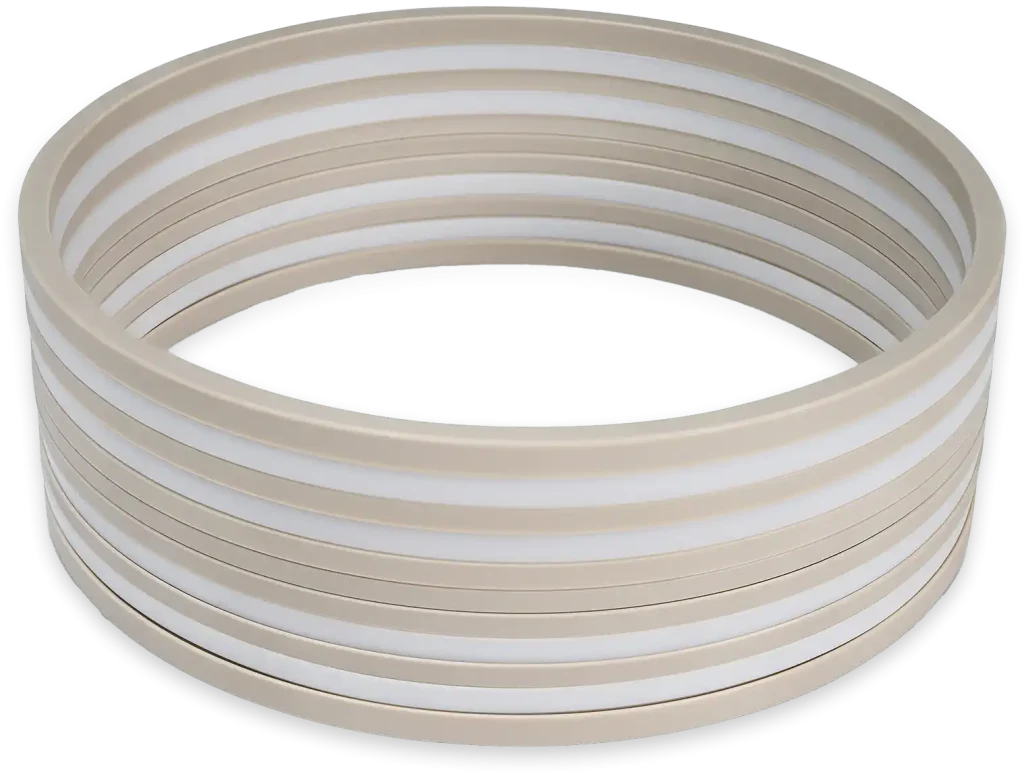
Seal Stacks for
Critical Applications
Our seals can be found in some of the harshest conditions in the world, servicing critical applications such as:
- Drilling Tools
- Wireline
- Casing Equipment
- Intelligent Completions
- Artificial Lift
- Subsea
- Completion
- Subsurface Safety Valves
- Subsurface Flow Controls
- Isolation Barrier Valves
- Liner Hangers
- Packers
- Frac/Toe Sleeves
- Multilaterals
- Sand Control
Polymer-Based Sealing Components
At MDS, we offer a variety of polymer-based sealing components designed to withstand critical situations in life-or-death environments. We offer polymer-based sealing components such as:
PETROZ
- FFKM Perfluoroelastomer
- Low Compression Set
- RGD Resistant
AFLAS
- Compounds Based on 100H Polymer
FKM
- Fluoroelastomer
- RGD Resistant
PEEK
- All Grades and Unique Compounds Developed by MDS
PPS
- All Grades Commonly Used in Oil & Gas Applications
PTFE
- All Grades
HNBR
- Hydrogenated Nitrile
RGD Resistant
Custom Seal Solutions
SES is orientated in the middle of the system to prevent damage (versus being on the ends) while CF PEEK end rings help reduce extrusion due to HP. Excellent for stab-in requirement.
Cross port applications: bonded center rubber to PEEK V-rings prevents rubber getting snipped from the ports; velocity rings protect the seals from high fluid flow.
V-Ring Bidirectional Seal System
Made of rubber, PTFE, or PEEK (depending on requirements).
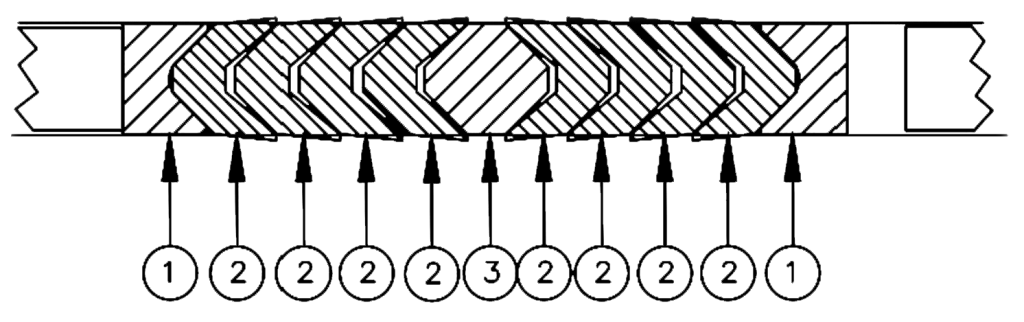
V-Ring Seal System with O-Ring
Bidirectional, low pressure sealing where the O-ring is protected by the V-ring to eliminate gaps.
- Advantages of V-Ring Seal Systems with O-Rings
- Combination of PEEK, PTFE, and elastomeric V-rings eliminates the disadvantages of compression set due to thermal cycling
- Rubber V-rings have a higher sealing force vs O-rings due to geometry
- Disadvantages of V-Ring Seal Systems with O-Rings
- Rubber V-rings require tooling
- 2-piece gland
V-Ring Seal System (Non-Elastomeric Spring Energized)
Bidirectional, capable of large delta T, chemically inert, spring energized primary seals keep the vee rings energized.
- Advantages of V-Ring Seal Systems (Non-Elastomeric Spring Energized)
- Less friction
- Spring energizer
- Non-elastomeric (no tooling)
- No chemical compatibility issues
- Disadvantages of V-Ring Seal Systems (Non-Elastomeric Spring Energized)
- 8-16 RMS
- 2-piece gland
- More expensive due to SES and adding components for hat rings